The Influence of 3D Printing Parameters on Adhesion between Polylactic Acid (PLA) and Thermoplastic Polyurethane (TPU)
《3D打印参数对聚乳酸(PLA)和热塑性聚氨酯(TPU)粘合力的影响》
作者:Emila Brancewicz-Steinmetz, Jacek Sawicki*, and Paulina Byczkowska
转自:
https://www.mdpi.com/1996-1944/14/21/6464
来源:
Materials 2021, 14(21), 6464
文章来源网络 如有侵权 请联系删除
Article source network, if there is infringement, please contact delete
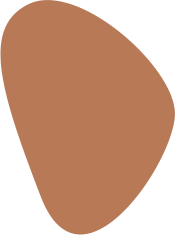
Part 01/
摘要
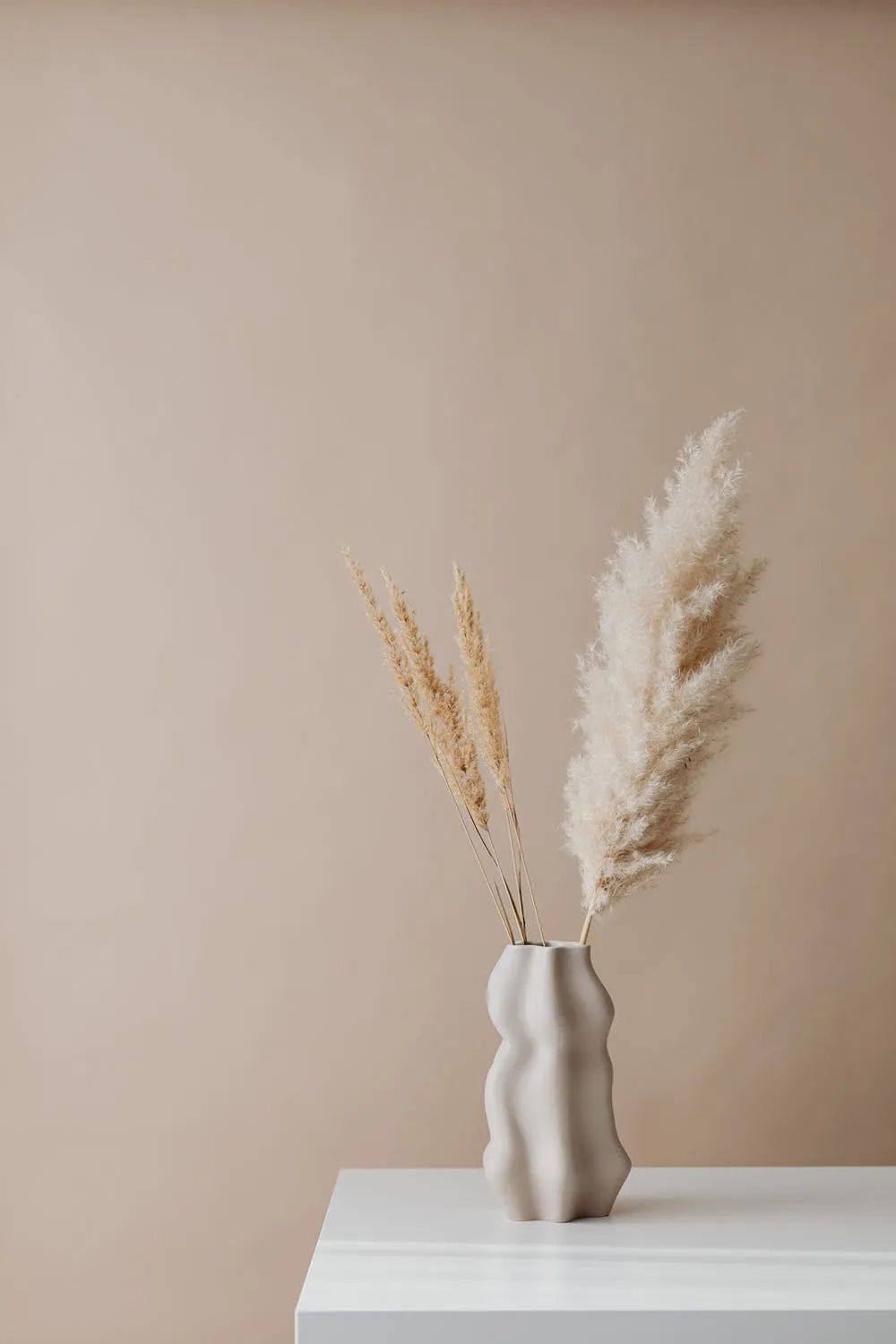

采用FDM技术的3D打印机允许使用两个喷嘴进行打印,这为生产多材料元素创造了机会。两种材料打印需要特别考虑在它们的几何边界之间产生的界面区域。本文旨在介绍使用市售长丝和软件,将PLA和TPU打印的可能性,以获得两种不同聚合物之间关于印刷参数、表面图案(由于材料接触表面的粗糙度)和层应用顺序的最佳粘合强度。通过为每种方案打印七个复制品来测试两种不同细丝(PLA-TPU和TPU-PLA)和六种图案组合的两个表面界面处的相互作用,共获得了12种组合。通过分析成对的样品(相同的图案,不同的材料顺序)发现,TPU/PLA样品的结果更好或非常接近PLA/TPU的结果,区分了模式组合的最佳变体。与组件材料相比,精心选择的打印参数可以防止零件效率降低(取决于材料组合)。
关键词:
FDM;多材料打印;粗糙度;剪切强度;热塑性聚氨酯;PLA
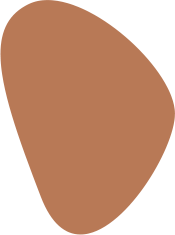
Part 02/
介绍

快速原型制作是一种很有前途的方法,可以支持模型和原型的高效生产[1,2,3]。增材制造(AM)技术允许获得具有可调整几何形状和机械性能的组件[4,5,6],可用于各种工业部门[7]。熔融沉积成型(FDM),也称为熔丝制造(FFF),是一种基于挤出的AM工艺。根据切片模型[8,9,10,11,12,13,14],材料作为灯丝被熔化并通过精细喷嘴层层选择性地分配。
FDM技术允许使用热塑性材料进行打印。聚乳酸(PLA)材料是一种可生物降解的材料,在打印大尺寸模型时具有低收缩率和良好的稳定性[9,15,16,17]。热塑性聚氨酯(TPU)是用途最广泛的工程热塑性塑料之一,具有弹性[18,19,20,21]。TPU是一种线性聚合物链通过共价键连接柔性和刚性链实现直线的材料[22]。TPU是一种具有高性能和电流消耗水平的弹性弹性体,可以提供一系列物理性能组合,可适应多种用途[23]。相关文献中已经研究了TPU与PLA的组合。
热塑性聚氨酯和聚乳酸颗粒通过热层压混合,有助于获得不同的形态结构和更好的形状记忆效应[24]。通过溶剂浇铸技术生产共混物证明了生产基于TPU和PLA共混物的生物相容性支架的可行性,该方法具有在组织工程中应用的潜力[25]。考虑到FDM 3D打印方法,可以选择制备由TPU和PLA组成的定制灯丝;较高的TPU含量会导致更出色的拉伸韧性。当使用现成的灯丝进行打印时,应选择适合材料的打印参数[16],并使用一个打印喷嘴进行标准打印。
Hu等人[26]研究了用于形成疝网的聚合物混合物,这表明人们对在添加剂生产中结合聚合物的可能性越来越感兴趣。PLA,由于其生物相容性,被用于生物医学。Liu等人[27]通过添加TPU对PLA进行改性,这种修改增加了电纺纤维的弹性,研究表明了其良好的形态、亲水性和高生物相容性。在3D打印中,Yoojung等人[28]对纱线的形状和成分进行建模,并用PLA和TPU纤维生产,显示出TPU纤维具有更好的弹性。因此,这些方法在服装行业具有广泛应用的潜力。
FDM技术中的3D打印机允许使用两个喷嘴进行打印,这为生产多材料元素创造了机会[1,2],使用两种材料打印需要特别考虑在它们的几何边界之间产生的界面区域。Lopes等人已经证明了从两个挤出头打印的相同材料之间的几何边界界面的负面影响,材料之间缺乏化学亲和力会使性能减弱,并且杨氏模量和拉伸强度的下降更为显著[29]。一种以上的材料打印可以创建多色元素并获得弹性机械性能,这可能有助于解剖建模和软机器人等领域[30,31,32,33,34]。正如Tamburrino等人证明的那样,层间粘合强度受印刷材料顺序、填充物、工艺温度和切片参数的影响[35]。按照FDM打印,作为一种分层的生产方式,建筑部件的表面光洁度难免比较粗糙,这个问题在FDM工艺在不同行业的广泛应用中被提出[36]。研究并提出了提高FDM 3D打印表面光洁度的解决方案。Anitha等人表明,层厚度对表面粗糙度的影响大于速度沉积和道路行程参数。Garg等人研究了以不同方向打印的零件的蒸汽处理过程,所有这些都有助于提高组件的表面光洁度[37]。Ahn等[38]提出了精细预测表面粗糙度表达式的方法。
根据对汽车行业实施的日益严格的环境法规和石化资源的预期枯竭,人们正在寻求环保的替代解决方案,使用下一代生物塑料和生物复合材料作为新型车辆部件的兴趣不断增加。为了与石油来源的塑料竞争,必须改进PLA的性能。PLA的持久应用受到其固有脆性的明显限制[39,40]。在一个过程中结合两种材料的可能性会影响添加剂的生产和印刷品更好机械性能的实现。然而,挑战在于令人满意的层间连接,本文已对此进行了分析。3D打印提供了广泛的个人和医疗保健产品(例如,具有抗切割特性的元素[41],聚合物的组合可用于在衣服上形成保护屏障,因此提供保护和防滑性[42,43]。
使用多种材料的增材制造有助于为许多行业中使用的组件提供更直接、更快和更高效的生产流程。一步生产过程中的多材料打印可用于任何需要机械强度、抗损坏性、减振以及可塑性的地方。PLA相的硬度可以确保负载吸收,而较软的TPU相可以限制裂纹。
使用增材制造方法可以创建特定模型,并且可以根据预期预测和修改元素表面。本文旨在介绍使用市售灯丝和软件,对PLA和TPU进行打印的可能性,以获得两种不同聚合物之间关于印刷参数和表面图案的最佳粘合强度(由于材料接触表面的粗糙度和层应用的顺序)。

Part 03/
材料和方法
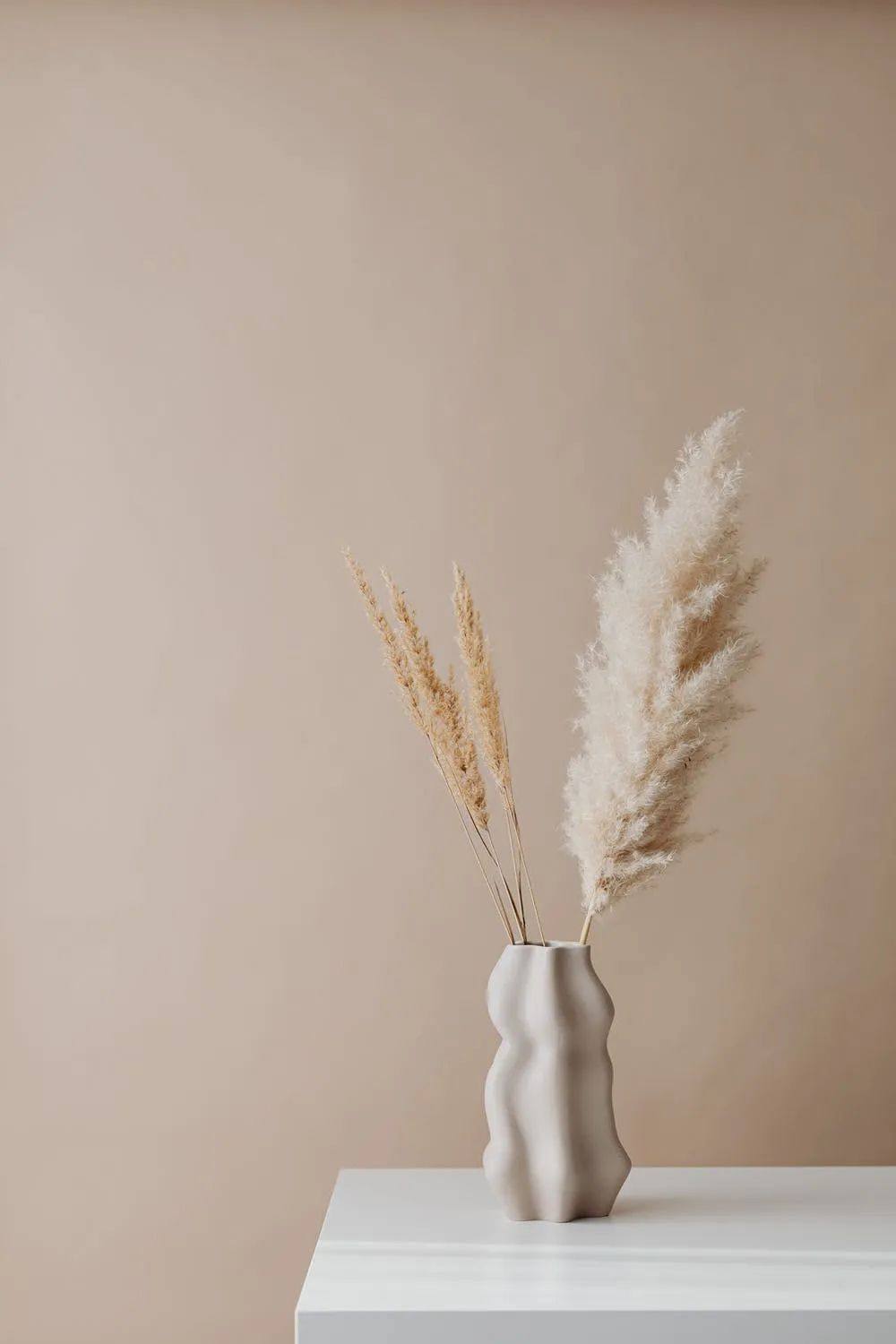
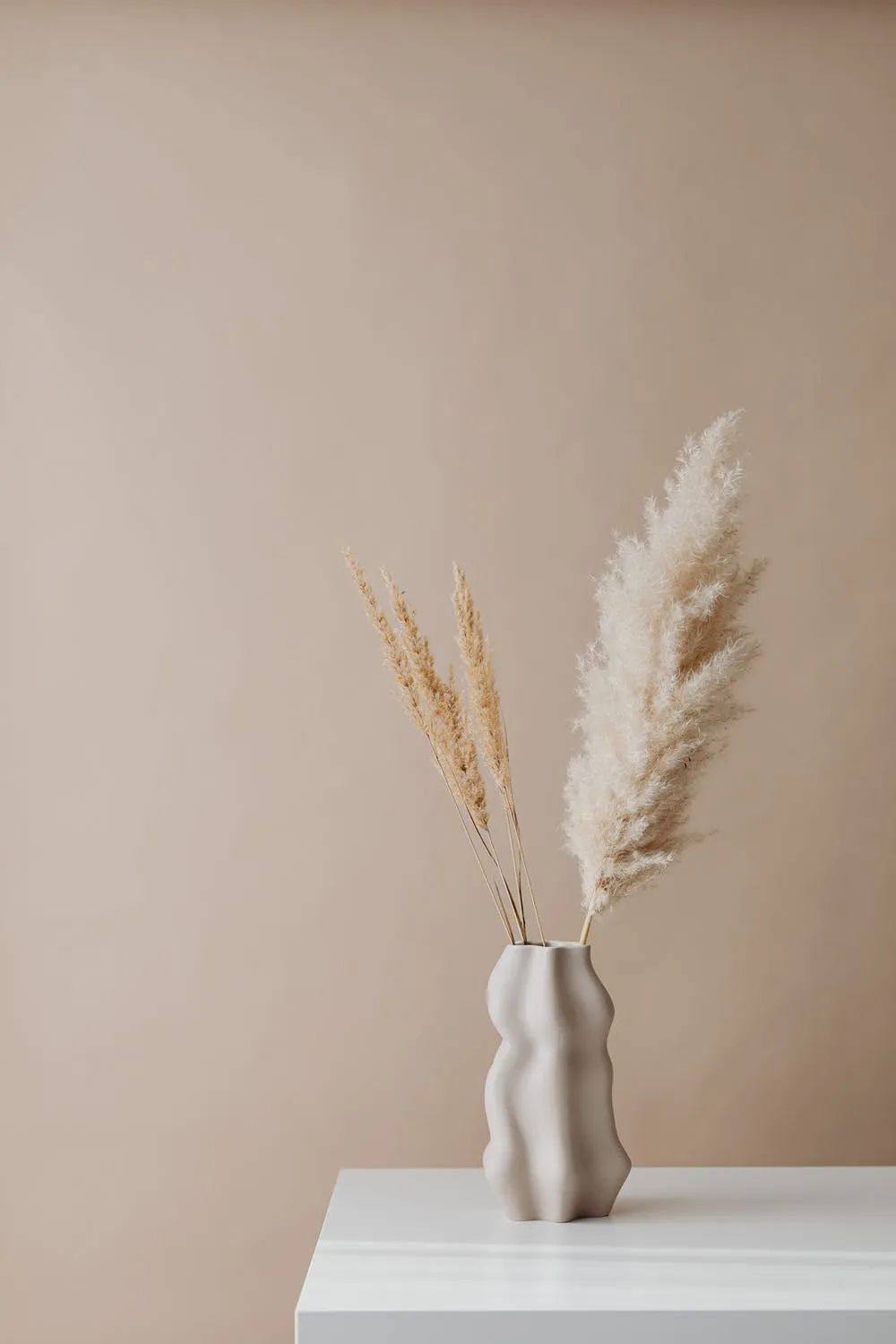
材料
在测试中,使用了直径为2.85mm的Ultimaker PLA red-RAL 3020和Fillamentum Flexfill TPU 98A Natural长丝。参考技术数据表,长丝的机械性能如表1所示。
表1. PLA和TPU的机械性能,参考技术数据表[44,45]
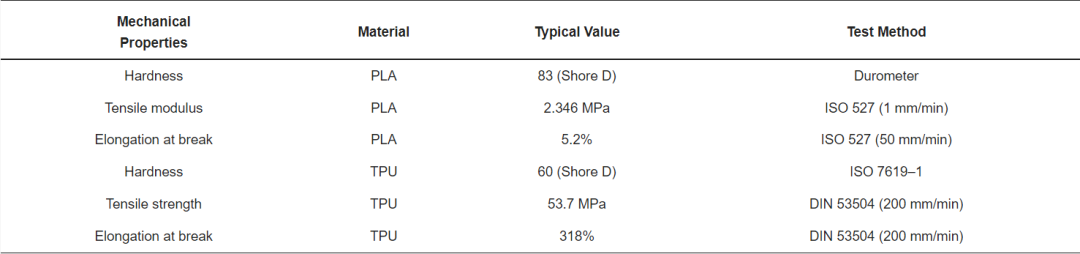
样品
使用带有SpaceClaim模块(Ansys Inc.,Canonsburg,PA,USA)的Ansys Workbench软件创建了3D模型。图1所示的模型由两个实体图(用于表示剪切强度测试的同轴圆柱体)组成。
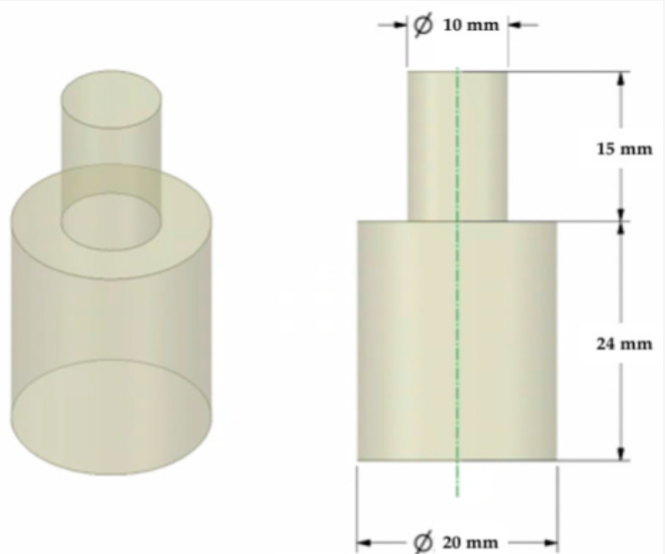
图1. 用于剪切测试的样品的3D模型
为了使用3D打印方法研究两种材料的最持久连接,改变了表面层图案。使用Cura软件对外部层进行了修改。该文件与样本的两部分中的每一部分一起上传到Cura软件。为每个部分设置打印参数,随后将两个部分合并形成一个样本。使用两种不同的配置来检查粘合强度对材料打印顺序的影响(图2)。每个样品的模型具有指定的表面层条件,打印成两个版本。一个版本由一个系列组成,七个相同的样品在一个系列中打印。
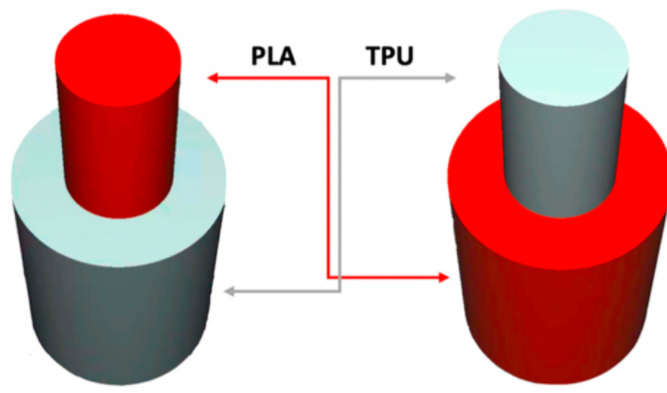
图2. 每种图案配置的材料打印顺序
2.3. 打印参数
使用带有两个喷嘴的Ultimaker 3D打印机和用于生成指定打印参数的Ultimaker Cura软件运行实验测试。两个挤出头中使用的喷嘴的模具直径为0.4毫米。PLA灯丝放置在打印机的第一个位置,TPU放在第二个位置。所有样品的印刷参数都是恒定的(表 2),不包括表面层,其中顶部和底部图案发生了变化。
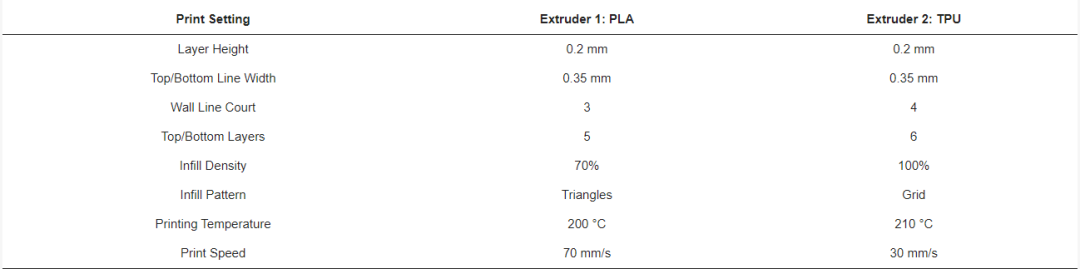
表2. 打印参数
涉及界面粘附的层是顶层和底层。Ultimaker Cura软件允许三种不同的顶部和底部图案:线条、同心和之字折线。这项研究比较了两种模式:不同配置的线和同心。通过打印机喷嘴施加第二材料层的配置和方法的示例如图3所示。
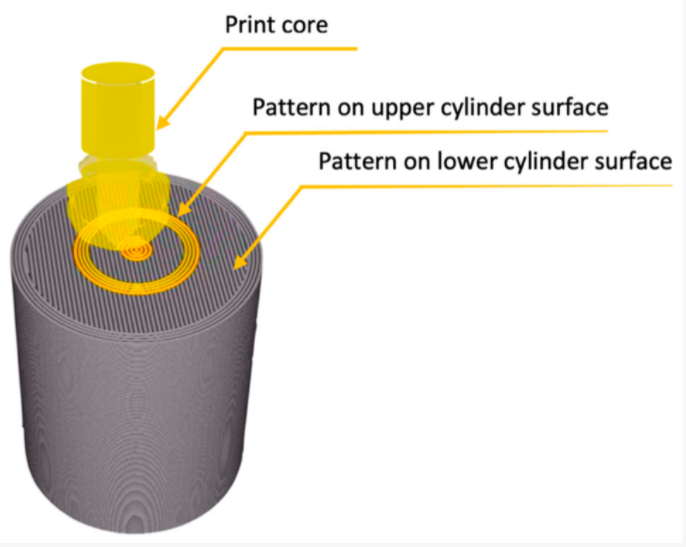
图3. 线材通过Print core的应用路径,该方案显示了上筒第一层的应用;在Cura软件(图层视图)中获得的图像
打印参数指定TPU和PLA的外壁层数、壁数和填充物。PLA的外部层数固定为5,TPU的外部层数固定为6,以便重点关注每层中使用的图案的影响。PLA的外壁打印成三行,TPU的外部打印成四行。使用PLA的70%填充密度和TPU的100%密度打印中间层。然而,外壁和顶层/底层总是以100%填充打印。样品的壁和层配置的图形可以在图4中看到。
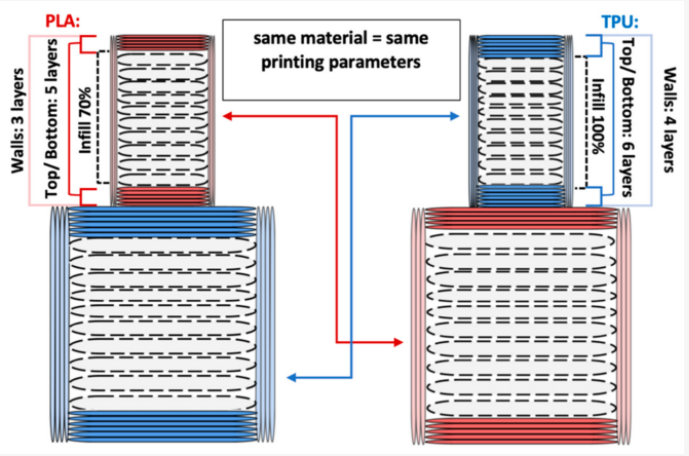
图4. 示例配置的图形表示。每个部分分为三个区域:外壁、顶层/底层。两种材料的中间填充物:热塑性聚氨酯(蓝色)和聚乳酸(红色)
外层是样本平面顶部和底部的元素,形成围绕填充物的一系列层。外壁是打印的外部部分,围绕着每一层的圆柱体的圆周。TPU和PLA的外层数不同。添加了一层额外的TPU,以实现更好的表面图案映射和开发,这是由于材料的特性和可塑性而进行的。
样品以六种图案配置打印,每种配置有两种材料版本(图2和图4)。表3列出了具有受力点变体、图案配置和打印样本数量的样本3D模型列表。
表3. 具有受力点变量、图案和材料配置以及打印样本数量的打印部件的3D模型
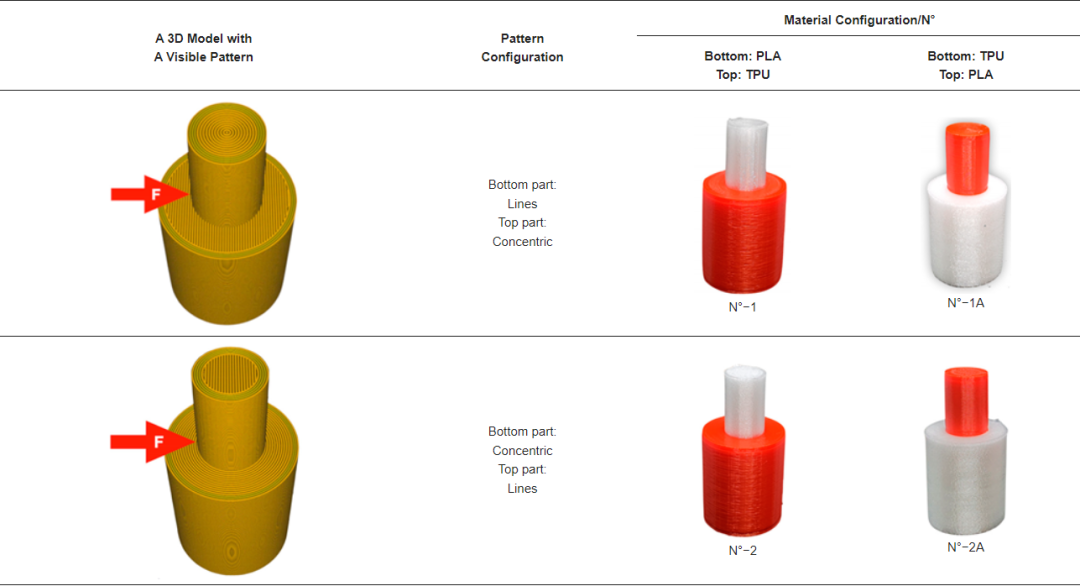
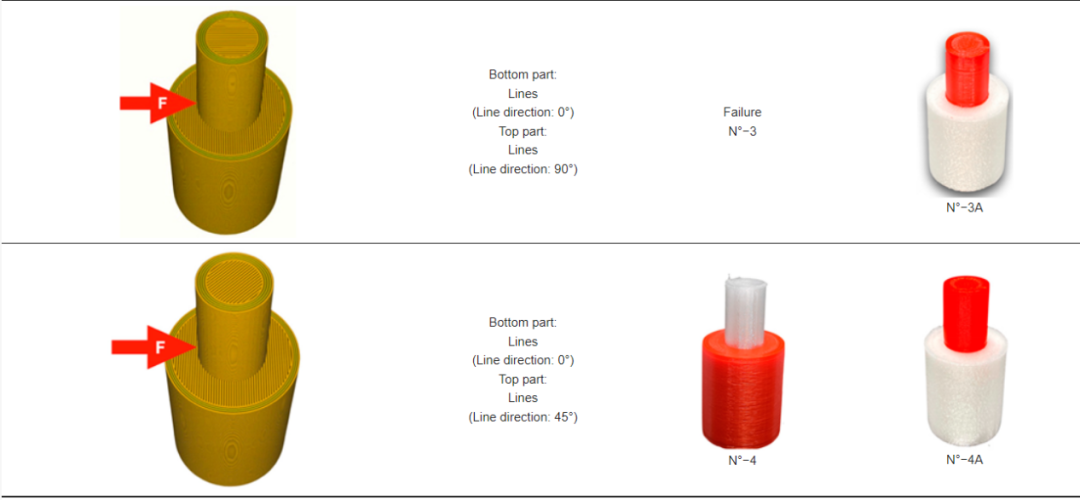
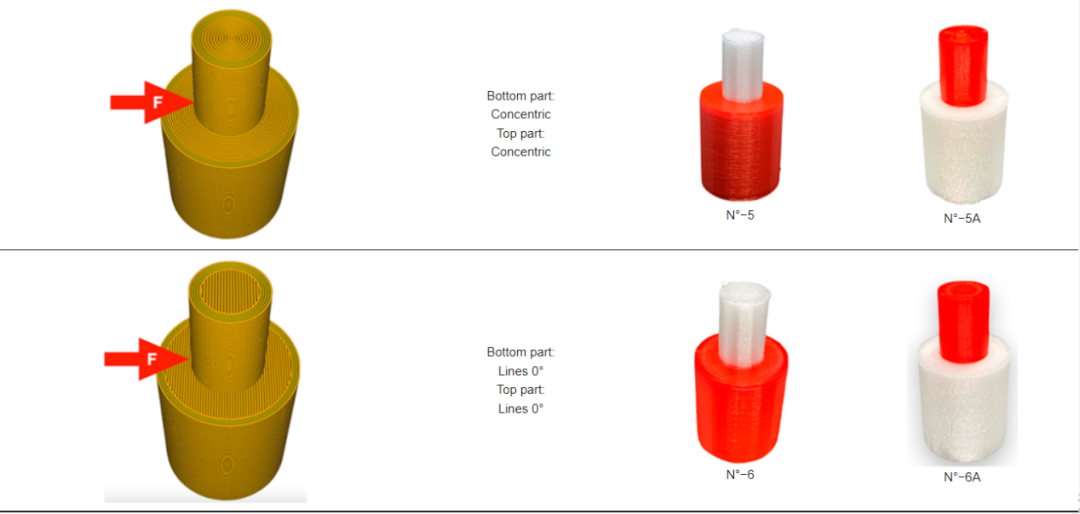
附着力
根据硬质泡沫塑料规则(ISO 1922:2018),剪切试验(图5)在通用试验机(来自 Zwick/Roell)上进行。机刀位移速率设置为1mm/min(在推荐范围内)。在研究两种聚合物之间的粘合强度时,按照J. Taczała等人的描述进行了附着力测试[46]。此外,每个表面图案配置都根据其直接在圆柱表面上的图案来分析影响它的力载荷。当下圆柱表面有线条图案时,垂直于该图案施加力载荷。当下圆柱上有同心图案而上圆柱有线条时,力垂直于上圆柱表面上的图案施加。当两个圆柱体上出现同心图案时,在不参考方向的情况下施加力。
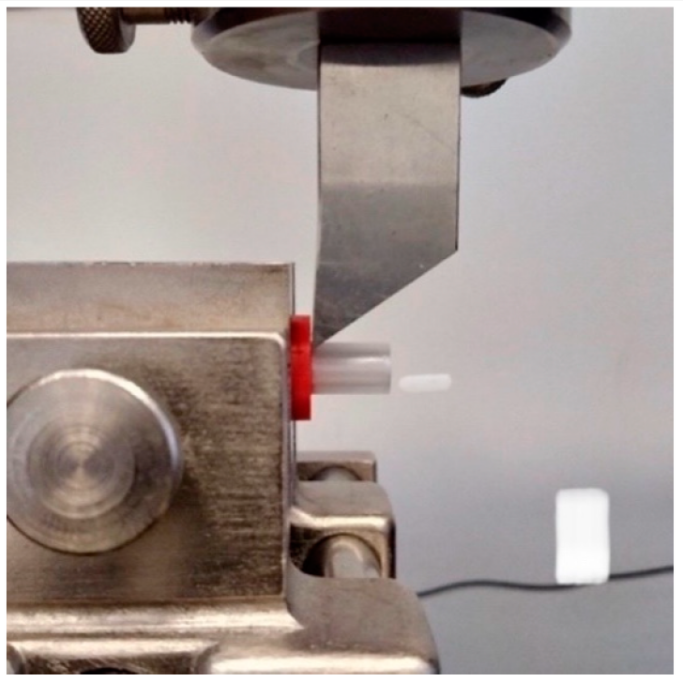
图5. 附着力测试的设置是使用剪切试验机进行的,放置的样品由PLA作为底部,TPU作为顶部圆柱体
粗糙度
为了测量样品的粗糙度,为每个图案额外打印了较低的样品圆柱体。创建了四个独立样本,带有线条和同心图案的TPU圆柱体和带有线条和同心图案的PLA圆柱体。使用 Hommel-Etamic T8000并根据PN-EN ISO 4287:1999测量粗糙度。测量装置如图 6a所示,测量是在从样品边缘(不包括外壁)到中心的4mm映射距离处进行的,垂直于图案线(图6b)。
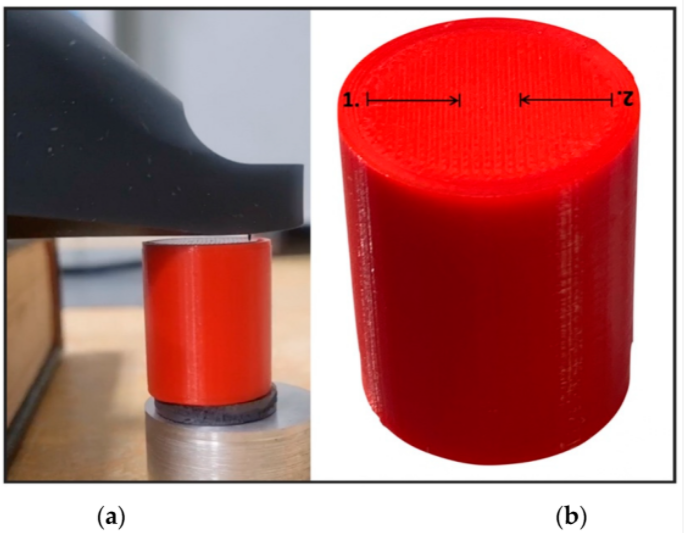
图6. (a)粗糙度测试装置;(b)粗糙度测量期间的映射距离

Part 04/
结果
以两种方式测试样品:研究下圆柱体外表面的粗糙度和测试聚合物表面之间的附着力。通过测量获得的数据使用单因素方差分析测试统计显著性进行测试,假设水平为p<0.05。统计分析是确定平均值和中位数以及标准差(SD)。
附着力
两种不同长丝(PLA-TPU和TPU-PLA)和六种图案组合的两个表面界面处的相互作用通过为每一种打印七个复制品进行测试;总共获得了十二种组合。不幸的是,尝试打印具有角线图案位移的样本(N°-3)-作为底部(PLA)交互表面角度为0°的线条图案和作为顶部(TPU)交互表面90°角的线条图案-失败了。为打印这些样本进行了四次尝试,但每次都失败了。失败可能与材料与接触表面上的图案的粘附力不足有关。不过,在应用第一个TPU层时出现了问题:材料从样品上脱落并拖到喷嘴上。在打印剩余批次的样品时,没有观察到类似的偏差。
从每个系列样品的五次测量(极端结果被拒绝)获得的算术平均值汇编如图7所示(最大力),而图8显示了剪切强度,图9显示了位移。

图7. 11个系列样品的最大力概览(图案和材料顺序的不同配置)
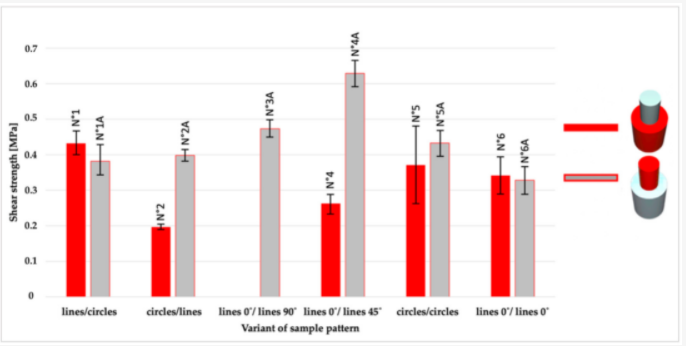
图8. 11个系列样品的平均剪切强度概览(图案和材料顺序的不同配置)
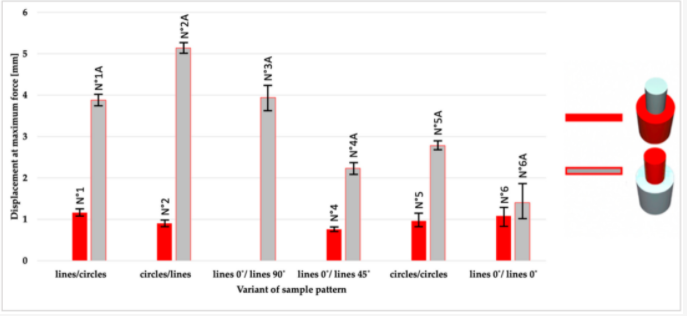
图9. 11系列样品的平均位移概览(图案和材料顺序的不同配置)
粗糙度
分析了两个轮廓粗糙度参数:Ra,作为峰谷之间的平均长度以及采样长度内表面上与平均线的偏差;Rz,作为在五个采样长度内从最高峰到最低谷的垂直距离,并将该距离平均[47]。
图10显示了结果:不同样品TPU和PLA的Ra(图10a)和Rz(图10b)粗糙度,外表面有线条和圆形。

图10. Hommel-Etamic T8000根据PN-EN ISO 4287:1999测量的粗糙度结果(a)以微米为单位的Ra参数 (b)以微米为单位的Rz参数
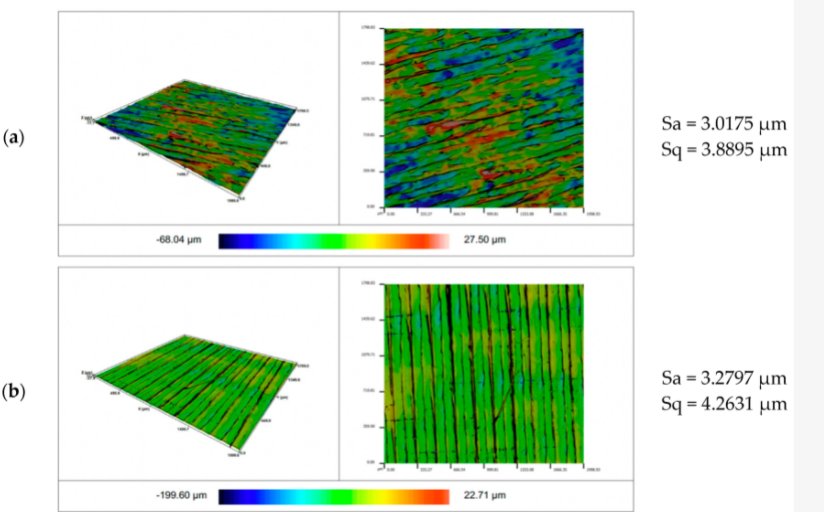
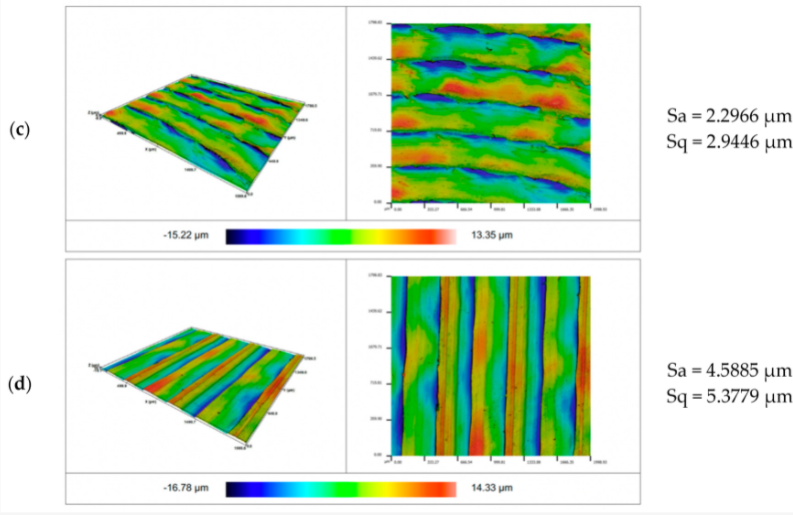
图11. 采用不同图案和材料配置制成的表面粗糙度等轴测图:(a)TPU圆;(b)TPU线;(c)PLA圆;(d) PLA线
粗糙度和附着力总结
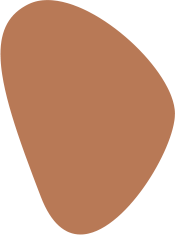
图12. 每种图案和材料组合的粗糙度(Ra)和剪切强度之间的关系

Part 05/
讨论
多材料打印允许在一个步骤过程中使用不同的灯丝来打印零件。他们正在分析导致创建具有特定属性的多功能部件的可能性。然而,多种材料打印将不可避免地导致不同材料之间产生边界界面。
为了拓宽对边界表面的理解,本文描述了一项研究,探讨了粗糙度对聚合物对之间粘合强度的影响。检查了以下方面:用于顶层/底层的图案和打印材料。测试了两组材料(PLA-TPU和TPU-PLA),每组有六种不同的图案配置。结果表明,由于材料接触表面的粗糙度,印刷顺序和表面图案会影响粘合强度。
条形图(图7)说明了所有样品系列的最大力N,因此表明最显著的力施加到样品N°1(具有线条/同心图案的PLA/TPU)。此外,对具有相同材料配置但图案相反的样品施加较小的力:N°2(具有同心/线条图案的PLA/TPU)。该图显示(图7)TPU/PLA样品系列获得的值,无论图案如何,都是相似的,这与印刷顺序颠倒的样品不同(PLA作为底部圆柱体,TPU作为顶部)。结果证实了这一点:TPU/PLA样品为4.75,而PLA/TPU为12.51。可以得出结论,无论图案如何,在TPU上打印比在PLA上打印更容易预测。
剪切强度,如图8所示,显示了在接触表面上具有不同图案组合的每对样品的值。通过分析成对的样品(相同的图案,不同的材料顺序),TPU/PLA样品的结果更好或接近 PLA/TPU样品的结果。算术平均值证实了这一点:TPU/PLA-0.39MPa,而 PLA/TPU-0.37MPa。
随后,提出了最大力下的位移。在所有样品对中,TPU/PLA样品的值(平均3.4 mm)明显高于PLA/TPU(平均1.49mm)。由于材料的硬度(邵氏D:TPU-60,PLA-83),剪切试验的结果证明了塑性和粘合强度之间的关系。在测试期间(在TPU/PLA样品上)将刀放在上PLA圆柱体上。当施加力时,TPU材料发生塑性变形,这导致更高的位移值。
测试了四种样品变体的粗糙度。下圆柱PLA和TPU上有四种可能的图案,具有同心和线条图案。热塑性聚氨酯样品的表面粗糙度较低(图10)。如图12所示,粗糙度对粘合强度没有直接影响。区分了模式组合的最佳变体:
No5A:同心花纹TPU—同心花纹PLA模式
No4A:具有0°线条图案的TPU — 具有45°线条图案的PLA模式
No5:同心纹PLA——同心纹TPU模式
No1:带有线条图案的PLA——带有同心图案的TPU模式
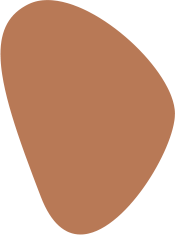
Part 06/
结论
该研究揭示了两种热塑性聚合物在3D打印过程中表面开发的最佳组合,这种组合在破坏性剪切试验中达到了最佳强度。由于附着力、打印参数、尺寸和样品几何形状之间的强依赖性,计划研究PLA热塑性聚合物与TPU在3D打印中的组合。未来的研究将集中在影响连接质量的打印参数、工艺温度和其他几何形状的样品中材料连接上,同时考虑样品的强度、拉伸和弯曲测试。
FDM 3D打印的显著优势是打印速度快且具有几何纬度的可选性。3D打印正在发展,创造了同时使用多种材料进行更快、一步生产的可能性。多材料打印需要精心设计模型构建、预测材料连接的质量以及改进方法,这样的研究拓宽了不同长丝粘合的知识,并促进了模型设计的工作。与组件材料相比,精心选择的打印参数可以防止零件效率下降,这最终取决于材料的组合。
转自:
https://www.mdpi.com/1996-1944/14/21/6464
参考文献:
1.Liu, Y.; Chen, J.; Shang, E.; Chen, Y. Process based modeling of energy consumption for multi-material FDM 3D printing. Chin. J. Mech. Eng. 2020, 20.
2.Yadav, D.; Chhabra, D.; Garg, R.K.; Ahlawat, A.; Phogat, A. Optimization of FDM 3D printing process parameters for multi-material using artificial neural network. Mater. Today Proc. 2020, 9, 1583–1591.
3.Anitha, R.; Arunachalam, S.; Radhakrishnan, P. Critical parameters influencing the quality of prototypes in fused deposition modelling. J. Mater. Process. Technol. 2001, 118, 385–388.
4.Garzon-Hernandez, S.; Garcia-Gonzalez, D.; Jérusalem, A.; Arias, A. Design of FDM 3D printed polymers: An experimental-modelling methodology for the prediction of mechanical properties. Mater. Des. 2020, 188, 108414.
5.Citarella, R.; Giannella, V. Additive Manufacturing in Industry. Appl. Sci. 2021, 11, 840.
6.Budzik, G.; Woźniak, J.; Paszkiewicz, A.; Przeszłowski, Ł.; Dziubek, T.; Dębski, M. Methodology for the Quality Control Process of Additive Manufacturing Products Made of Polymer Materials. Materials 2021, 14, 2202.
7.Kusoglu, I.; Doñate-Buendía, C.; Barcikowski, S.; Gökce, B. Laser Powder Bed Fusion of Polymers: Quantitative Research Direction Indices. Materials 2021, 14, 1169.
8.Popescu, D.; Zapciu, A.; Amza, C.; Baciu, F.; Marinescu, R. FDM process parameters influence over the mechanical properties of polymer specimens: A review. Polym. Test. 2018, 69, 157–166.
9.Haghsefat, K.; Eng, M.; Tingting, L. FDM 3D Printing Technology and Its Fundemental Properties. In Proceedings of the International Conference on Innovation and Research in Engineering Sciences, Tbilisi, Georgia, 30 June 2020.
10.Bergonzi, L.; Vettori, M.; Stefanini, L.; D’Alcamo, L. Different infill geometry influence on mechanical properties of FDM produced PLA. In IOP Conference Series: Materials Science and Engineering, Proceedings of the 49th AIAS Conference (AIAS 2020), Genova, Italy, 2–5 September 2020; IOP Publishing: Bristol, UK, 2021.
11.Buj-Corral, I.; Bagheri, A.; Domínguez-Fernández, A.; Casado-López, R. Influence of infill and nozzle diameter on porosity of FDM printed parts with rectilinear grid pattern. Procedia Manuf. 2019, 41, 288–295.
12.Yahamed, A.; Ikonomov, P.; Fleming, P.D.; Pekarovicova, A.; Gustafson, P.; Alden, A.Q.; Alrafeek, S. Mechanical properties of 3D printed polymers. J. Print Media Technol. Res. 2016, 5, 273–289.
13.Taczała, J.; Czepułkowska, W.; Konieczny, B.; Sokołowski, J.; Kozakiewicz, M.; Szymor, P. Comparison of 3D printing MJP and FDM technology in dentistry. Arch. Mater. Sci. Eng. 2020, 1, 32–40.
14.Lüchtenborg, J.; Burkhardt, F.; Nold, J.; Rothlauf, S.; Wesemann, C.; Pieralli, S.; Wemken, G.; Witkowski, S.; Spies, B. Implementation of Fused Filament Fabrication in Dentistry. Appl. Sci. 2021, 11, 6444.
15.Jeon, B.; Han, J.W.; Lee, K.S.; Cha, S.W. Improvement of the Mechanical Properties of Biodegradable Polymers Using a Microcellular Foaming Process and Natural By-Products. Polym. Technol. Eng. 2012, 51, 401–406.
16.Tao, Y.; Shao, J.; Li, P.; Shi, S.Q. Application of a thermoplastic polyurethane/polylactic acid composite filament for 3D-printed personalized orthosis. Mater. Teh. 2019, 53, 71–76.
17.Mamiński, M.; Novák, I.; Mičušík, M.; Małolepszy, A.; Toczyłowska-Mamińska, R. Discharge Plasma Treatment as an Efficient Tool for Improved Poly(lactide) Adhesive–Wood Interactions. Materials 2021, 14, 3672.
18.Lee, Y.-H.; Kang, B.-K.; Kim, H.-D.; Yoo, H.-J.; Kim, J.-S.; Huh, J.-H.; Jung, Y.-J.; Lee, D.-J. Effect of hot pressing/melt mixing on the properties of thermoplastic polyurethane. Macromol. Res. 2009, 17, 616–622.
19.Tabuani, D.; Bellucci, F.; Terenzi, A.; Camino, G. Flame retarded Thermoplastic Polyurethane (TPU) for cable jacketing application. Polym. Degrad. Stab. 2012, 97, 2594–2601.
20.Mrówka, M.; Szymiczek, M.; Machoczek, T.; Pawlyta, M. Influence of the Halloysite Nanotube (HNT) Addition on Selected Mechanical and Biological Properties of Thermoplastic Polyurethane. Materials 2021, 14, 3625.
21.He, X.; Zhou, J.; Jin, L.; Long, X.; Wu, H.; Xu, L.; Gong, Y.; Zhou, W. Improved Dielectric Properties of Thermoplastic Polyurethane Elastomer Filled with Core–Shell Structured PDA@TiC Particles. Materials 2020, 13, 3341.
22.Lee, H.; Eom, R.-I.; Lee, Y. Evaluation of the Mechanical Properties of Porous Thermoplastic Polyurethane Obtained by 3D Printing for Protective Gear. Adv. Mater. Sci. Eng. 2019, 2019, 1–10.
23.Sambruno, A.; Bañon, F.; Salguero, J.; Simonet, B.; Batista, M. Kerf Taper Defect Minimization Based on Abrasive Waterjet Machining of Low Thickness Thermoplastic Carbon Fiber Composites C/TPU. Materials 2019, 12, 4192.
24.Ji, X.; Gao, F.; Geng, Z.; Li, D. Fabrication of thermoplastic polyurethane/polylactide shape-memory blends with tunable optical and mechanical properties via a bilayer structure design. Polym. Test. 2021, 97, 107135.
25.Lis-Bartos, A.; Smieszek, A.; Frańczyk, K.; Marycz, K. Fabrication, Characterization, and Cytotoxicity of Thermoplastic Polyurethane/Poly(lactic acid) Material Using Human Adipose Derived Mesenchymal Stromal Stem Cells (hASCs). Polymers 2018, 10, 1073.
26.Hu, Q.; Suihong, L.; Yan, G.; Zhicheng, S. Topological Structure Design and Fabrication of Biocompatible PLA/TPU/ADM Mesh with Appropriate Elasticity for Hernia Repair. Macromol. Biosci. 2021, 21, 2000423.
27.Liu, X.; Zhou, L.; Heng, P.; Xiao, J.; Lv, J.; Zhang, Q.; Hickey, M.E.; Tu, Q.; Wang, J. Lecithin doped electrospun poly(lactic acid)-thermoplastic polyurethane fibers for hepatocyte viability improvement. Colloids Surf. B Biointerfaces 2018, 175, 264–271.
28.Han, Y.; Kim, J. A Study on the Mechanical Properties of Knit Fabric Using 3D Printing—Focused on PLA, TPU Filament. J. Fash. Bus. 2018, 22, 93–105.
29.Lopes, L.; Silva, A.; Carneiro, O. Multi-material 3D printing: The relevance of materials affinity on the boundary interface performance. Addit. Manuf. 2018, 23, 45–52.
30.Schwartz, J.J.; Boydston, A.J. Multimaterial actinic spatial control 3D and 4D printing. Nat. Commun. 2019, 10, 791.
31.Mohammed, M.I.; Tatineni, J.; Cadd, B.; Peart, G.; Gibson, I. Advanced auricular prosthesis development by 3D modelling and multi-material printing. In Proceedings of the International Conference on Design and Technology (DesTech 2016), Geelong, Australia, 5–8 December 2016; Volume 7. Available online: https://dro.deakin.edu.au/eserv/DU:30091544/gibson-advancedauricular-2017.pdf (accessed on 8 September 2021).
32.Yin, J.; Li, M.; Dai, G.; Zhou, H.; Ma, L.; Zheng, Y. 3D Printed Multi-material Medical Phantoms for Needle-tissue Interaction Modelling of Heterogeneous Structures. J. Bionic Eng. 2021, 18, 346–360.
33.Skylar-Scott, M.A.; Mueller, J.; Visser, C.W.; Lewis, J.A. Voxelated soft matter via multimaterial multinozzle 3D printing. Nature 2019, 575, 330–335.
34.Ge, Q.; Sakhaei, A.H.; Lee, H.; Dunn, C.K.; Fang, N.X.; Dunn, M.L. Multimaterial 4D Printing with Tailorable Shape Memory Polymers. Sci. Rep. 2016, 6, 31110.
35.Tamburrino, F.; Graziosi, S.; Bordegoni, M. The influence of slicing parameters on the multi-material adhesion mechanisms of FDM printed parts: An exploratory study. Virtual Phys. Prototyp. 2019, 14, 316–332.
36.Rahmati, S.; Vahabli, E. Evaluation of analytical modeling for improvement of surface roughness of FDM test part using measurement results. Int. J. Adv. Manuf. Technol. 2015, 79, 823–829.
37.Garg, A.; Bhattacharya, A.; Batish, A. On Surface Finish and Dimensional Accuracy of FDM Parts after Cold Vapor Treatment. Mater. Manuf. Process. 2016, 31, 522–529.
38.Ahn, D.; Kweon, J.-H.; Kwon, S.; Song, J.; Lee, S. Representation of surface roughness in fused deposition modeling. J. Mater. Process. Technol. 2009, 209, 5593–5600.
39.Bouzouita, A.; Notta-Cuvier, D.; Raquez, J.-M.; Lauro, F.; Dubois, P. Poly(lactic acid)-Based Materials for Automotive Applications. In Industrial Applications of Poly(lactic acid). Advances in Polymer Science; Di Lorenzo, M., Androsch, R., Eds.; Springer: Cham, Switzerland, 2017; Volume 282.
40.Bouzouita, A. Elaboration of Polylactide-Based Materials for Automotive Application: Study of Structure-Process-Properties Interactions Amani Bouzouita. Ph.D. Thesis, Université de Valenciennes et du Hainaut-Cambresis, Valenciennes, France, Université de Mons, Mons, Belgium, 2016.
41.Fort, T.; Bruns, K.; Bichel, A.; Miller, J.; Vanstrom, J.R.; Koziel, J.A. Puncture and Cut Resistant Glove Testing; TSM 416 Technology Capstone Projects. 31; Iowa State University Digital Repository: Ames, IA, USA, 2018.
42.Higher Dimension Materials, Inc. Cut, Abrasion and/or Puncture Resistant Knitted Gloves. U.S. Patent 20170055608, 2 March 2017.
43.Chari, S.; Haines, T.; Varghese, P.; Economidis, A. Are non-slip socks really ’non-slip’? An analysis of slip resistance. BMC Geriatr. 2009, 9, 39.
44.Filamentum, Flexfill TPU 98A, TDS. Available online: http://www.fillamentumautomotive.com/116/uploads/2020/10/Technical-Data-Sheet_Flexfill-TPU-98A_26082019.pdf (accessed on 16 August 2021).
45.Ultimaker PLA, TDS. Available online: https://support.ultimaker.com/hc/en-us/articles/360011962720 (accessed on 16 August 2021).
46.Taczała, J.; Rak, K.; Sawicki, J.; Krasowski, M. Numerical Analysis of the Bond Strength between Two Methacrylic Polymers by Surface Modification. Materials 2021, 14, 3927.
47.Surface Texture from Ra to Rz. Available online: https://www.mmsonline.com/columns/surface-texture-from-ra-to-rz (accessed on 16 August 2021).
以“新材料、新技术在鞋材领域的创新应用与提升”为着力点推出的《第五届鞋材新技术新产品研讨会》将邀请鞋材行业著名的鞋材生产企业、鞋材发泡相关生产企业、科研院校等一起研究探讨该领域的“黑科技”,为与会嘉宾呈现尼龙弹性体、TPU发泡、鞋材升级、产业发展趋势、3D打印鞋材等行业关注的热点及关键点等前沿技术和应用。
现将会议有关事项通知如下,欢迎热塑性弹性体鞋材产业链及相关研究机构、单位和企业报名参加。
中国合成橡胶工业协会热塑性弹性体(TPE)分会
山东道恩高分子材料股份有限公司
泉州市旭丰粉体原料有限公司
天津利安隆新材料股份有限公司
上海迪塔班克数据科技有限公司(俺搜)
三明市锦浪新材料科技有限公司
泉州华利塑胶有限公司
福建省鑫烨鞋材工贸有限公司
浙江众立合成材料科技股份有限公司
惠州李长荣橡胶有限公司
泉州市易斯特永隆新材料科技有限公司

会议主题
1.《创新低碳环保材料,赋能鞋业绿色发展》-张立群院士
2.《中国鞋材行业十四五发展展望》-路华
3.《近年来巴陵石化SBC在鞋材中的应用》-梁红文
4.《弹性体物理发泡技术及应用进展》-翟文涛
5.《超临界物理发泡和物理微球发泡的现状与前景》-秦柳
6.《中国产品现状及分析-鞋类产品应重视缺陷召回问题》-叶永和
7.《关于运动鞋功能性材料的研发思考》-甘舸
8.《弹性体材料在军事领域应用前景展望》-陈希真
9.《聚合物间歇式超临界流体发泡》-张振秀
10.《鞋底材料检验研究进展》-姜红
11.《从鞋类产品监督抽查结果分析鞋底材料常见质量问题与发展对策》-张海煊
12.《解读化塑产业数字化大趋势》-柯廷文
13.《苯乙烯类热塑性弹性体结构、性能与展望》-韩丙勇
14.《生物基TPU材料与TPU环保发泡皮革在鞋材后段加工应用》-姜伟
15.《鞋用材料的抗老化解决方案》-尹芳芳
16.《新颖SBC发泡发展》-黄玮勤
17.《金属3D打印引领制鞋行业新技术革新》-朱姚胜

会议费用
1.会务费:会员单位1000元/人;非会员单位2100元/人;未缴纳本年度会费的会员单位收费标准等同非会员单位;申请入会请与会务组联系。
2.未缴纳2022年热塑性弹性体(TPE)分会会费的会员单位可现场缴费。
3.疫情期间为方便会场管理,请提前缴纳会务费。
账户名称:中国合成橡胶工业协会;
开户银行:中国工商银行北京六铺炕支行;
收款账号:
0200022309014445442;
转账请备注“鞋材会议+参会人及手机号”。
交通、住宿费用自理;住宿费用直接交给酒店,由酒店开具住宿发票。
市场推广
1.会议赞助、会议推介报告、大屏幕滚动广告、展示台、易拉宝、手提袋广告、资料入袋、会刊插页、代表证及纪念品等与会务组联系;
2.会议期间不允许自行宣传。
特别说明
2.已经报名的参会代表保留原定的会议权益;未报名的行业同仁可识别下方报名二维码提交参会意向并及时缴费。因场地原因,剩余报名名额有限,达到一定报名数量后报名通道关闭,欲报从速。
联 系 方 式:
会议相关事宜请电话联系会务组:
刘经理:18801122364
付经理:18813039317
座机:010-53350693
E-mail:tpe@cnsria.org.cn

嘉宾阵容

TPE分会秘书处为本次鞋材会议精心编制了内容详实、印刷精美的《第五届鞋材新技术新产品研讨会TPE分会技术资讯汇编》, 所有提前进行会议注册的参会嘉宾都将现场获赠该技术汇编。
TPE分会介绍
TPE分会公众号
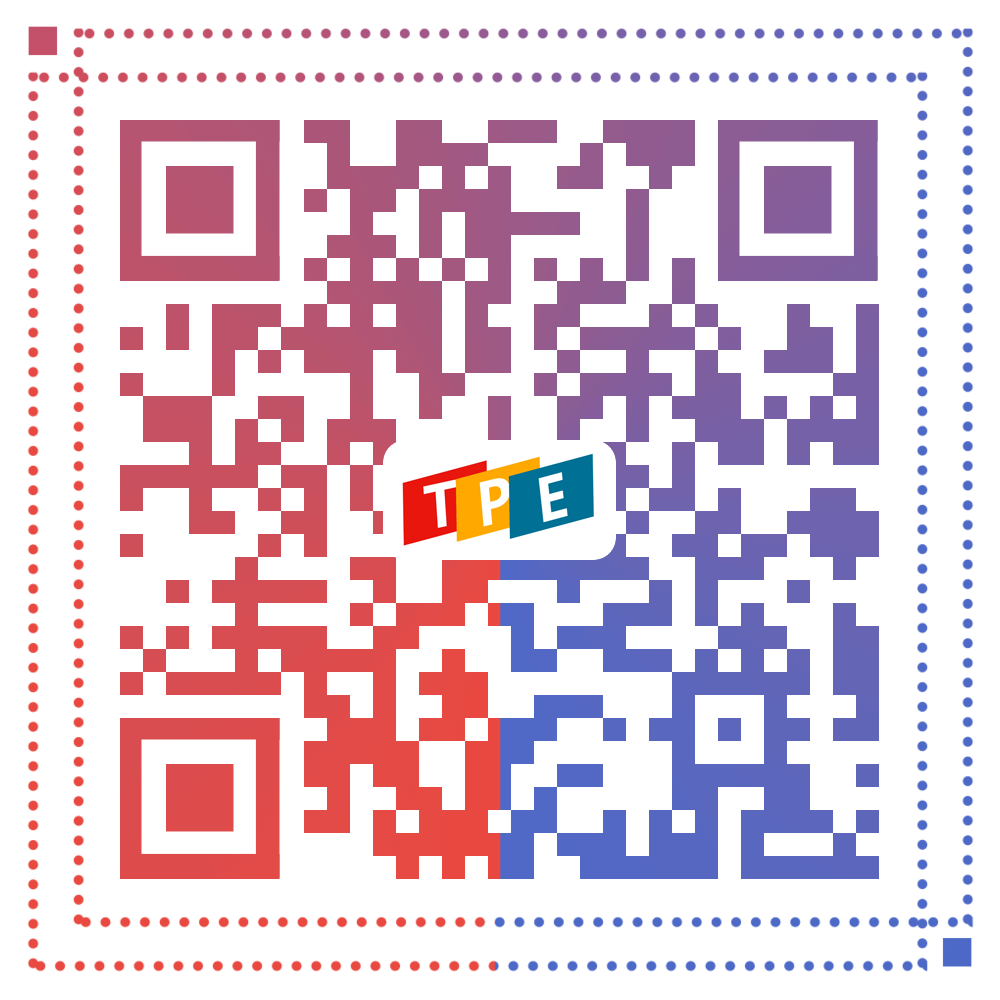
扫码加入我们
部分支持单位风采:
推荐阅读:
6. 热塑性弹性体的气压热性能
原文始发于微信公众号(TPE分会):《3D打印参数对聚乳酸(PLA)和热塑性聚氨酯(TPU)粘合力的影响》
